
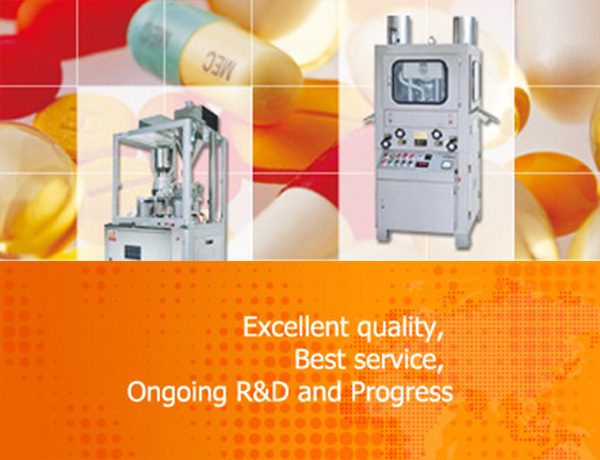
This still designed to meet to USP specification of water for injection, meantime acording to water quality differ from feed water and different number of effects, the distillate resistivity quality easy to obtain and the distillate temperature id over 80°C to avoid bacteria growing. The feed water at least is better than Deionized Water (DIW).
This equipment is take advantage of heat exchanger working principle, just first column is heated by an extermal steam, other column is from the first column pure steam used for heating the next column, use evaporator and condenser to force the proceed two phase variation, detailed describing as following.
First, let evaporator inside feed water pass through heat exchanger change from liquid to vapor, use its latent heat into separator. In the separator inside is equip with special mist damper and high centrifugal force cyclone dervice. The vapor will passing through 180 degree continuous rotation, by means of above mentioned special dervice to separate particles, drops and pyrogenic, and so on the vapor of leaving separator is not contains solution solid and pyrogenic, it is sterile and pryogenation free. These particles and drops will return to the evaporator column low part to hearting again, here just high speed purified vapor can pass through the separator enter condenser. Then to processed second phase variation, let condenser inside vapor pass through cooling exchanger change from vapor to liquid (distillate), and use diverter valve to assure the distilled water quality, if the water quality is below purity set, it will exhaust to drain piping, otherwise it will flow to storage tank to provide with the pharmaceutical purpose of water for injection.
Moreover, due to this still is adopt multiple effect type and via first condenser to preheat the feed water before entering each column, meanwhile every column the evaporation inside feed water latent heat piping device is equip with recovery, to consumption of the steam energy.
Mode
|
Number
of
Effects |
5
Bar Steam Heating
|
Dimensions
|
|||||
Production
Capacity (Lt/hr) |
Steam
(kg/r) |
Cooling
Water (Lt/hr) |
Height
(mm) |
Length
(mm) |
Width
(mm) |
Weight
(mm) |
||
MS-250/4
|
4
|
250
|
85
|
280
|
280
|
2,500
|
1,300
|
800
|
MS-500/4
|
4
|
510
|
150
|
500
|
500
|
2,500
|
1,300
|
900
|
MS-500/5
|
5
|
510
|
130
|
300
|
300
|
2,500
|
1,450
|
1,000
|
MS-1000/5
|
5
|
1,200
|
320
|
600
|
600
|
2,900
|
1,900
|
2,000
|
MS-1000/6
|
6
|
1,200
|
270
|
600
|
600
|
2,900
|
2,240
|
2,300
|
MS-1500/5
|
5
|
1,700
|
420
|
750
|
750
|
3,200
|
3,040
|
2,700
|
MS-1500/6
|
6
|
1,700
|
350
|
750
|
750
|
3,200
|
3,350
|
3,000
|
MS-2000/5
|
5
|
2,200
|
620
|
1,000
|
1,000
|
3,200
|
3,000
|
3,300
|
MS-2000/6
|
6
|
2,200
|
550
|
1,000
|
1,000
|
3,200
|
3,430
|
3,800
|
MS-3000/6
|
6
|
3,200
|
700
|
1,200
|
1,200
|
3,700
|
3,900
|
4,800
|
MS-4000/6
|
6
|
4,300
|
1,000
|
1,400
|
1,400
|
3,900
|
4,480
|
6,800
|