
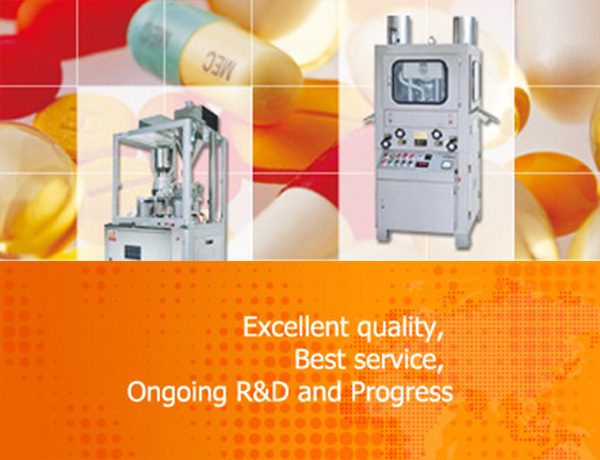
Model No
|
ACF-100
|
Capacity (caps/hr)
|
58,000~62,700
|
Capsule Size
|
#00,#0,#1~#4
|
Power Supply
|
220/380V 3Phase
50/60Hz |
Power Consumption
|
20.6 A
|
Main drive
|
2 HP
|
Auger drice
|
1/2 HP
|
Vacuum Pump
|
2 HP
|
De-duster
|
3HP*2 Pcs
|
Machine Weight
|
1200 KGs
|
Dimension |
983×1201×2013 mm (L×W×H) |